Product Overview
Cutback Bitumen is produced by lowering the thickness of regular bitumen through the inclusion of predominantly petroleum based solvent. Cutback Bitumen is utilized due to its lower viscosity compared to neat asphalt, making it suitable for use in applications that require low temperatures. Once the cutback evaporates, only the Bitumen remains. It is claimed that a cutback bitumen cures once the petroleum solvent evaporates. Cutback bitumen is commonly employed for prime coats and tack coats. Typically, they are categorized into three groups based on the solvent’s volatility that is included..
Generally are divided into three groups depending on their volatility of the solvent added:
·
Rapid Curing products
are prepared with a light, rapidly evaporating diluent such as a naphtha or
gasoline.
As a solvent required to produce a cutback
asphalt, it is possible to use not only the above described petroleum type
solvent but also a coal type solvent or may be a mixture of various solvents
and an additive in order to further improve the performance of final products
(e.g. antistripping effect).
·
Medium Curing are
a blend of Bitumen with lighter hydrocarbons such as kerosene.
Slow Curing, also known as “road oils,” are typically derived from the fractional distillation of specific crude petroleum and are a residual material. Typically, aromatic, naphthenic, and paraffinic oils are traditionally utilized. Blending bitumen with an oily petroleum fraction can be used to create slow curing liquid bitumen materials.
All six standard grades are produced for each of the three types of liquid asphaltic materials. Each grade is identified by a prefix which indicates the curing speed: SC for Slow Curing, MC for Medium Curing, and RC for Rapid Curing. The grade number, also known as the suffix, indicates the viscosity range of the substance. Grade 0 is the most fluid and grade 5 is the most thick in every category, with the middle grades varying in texture in a systematic order. Grade 0 materials have the consistency of heavy cream at room temperature, while grade 5 materials have the consistency of heavy molasses in cold weather. These items heal through the process of the petroleum diluent evaporating.
In the past, cutback asphalt mixtures were advantageous due to the lower temperature required for paving. Nevertheless, currently, cutback asphalt is primarily utilized as a prime coat and/or tack coat.
The cutback asphalt is applied to untreated subgrade or base layers as a prime coat, filling surface voids and protecting against water penetration, stabilizing fines, preserving subbase material, and promoting bonding with next pavement layers.
Cutback asphalt is applied as a tack coat between hot mix asphalt pavement lifts to encourage proper bonding. Ensuring proper bonding between construction lifts and the existing road surface and overlay is crucial for the pavement structure to function as one unit and have sufficient strength. If neighboring layers do not adhere to each other, they function as separate thin layers that are not built to withstand expected bending stresses from traffic. Insufficient adhesion between layers may lead to separation of layers (deboning) which can cause longitudinal wheel path cracking, fatigue cracking, potholes, and other issues like rutting that can significantly shorten the lifespan of the pavement.
Priming and Tack Coating
Priming entails the application of a thin binder with low viscosity to a prepared base of aggregate that is typically unbound. The goal is for it to be absorbed by the upper layers of the substrate and create a surface that can be more easily saturated by a following bituminous layer. The primer can temporarily handle traffic (although this is rare) and assist in dust control. Typically, primers are used in quantities ranging from 0.5 to 1.4 liters per square meter. Cutback bitumen that is appropriate for priming is also utilized for tack coats, which are applied to a base surface to improve the adhesion of the following asphalt layer. An average rate of application falls within the range of 0.2 to 0.4 liters per square meter.
Prime Sealing
If temperatures are too low for proper priming, or if there is heavy traffic that could damage the primed surface before the final seal is applied, a primer seal can be utilized to provide sufficient pavement protection for 6 to 12 months. Cutback bitumen, appropriate for primer sealing, can also be utilized in creating pre-mix asphalt for patch repairs.
Spray Sealing
Cutback bitumen is commonly utilized in sprayed sealing projects, especially in colder temperatures to enhance initial stone retention with its reduced viscosity. Normally, one coat of the correct cutback bitumen is sprayed onto the primed pavement before the aggregate is applied.
Rapid Curing Cutback Bitumen Specification (ASTM D2028 or AASHTO M81-92 2008)
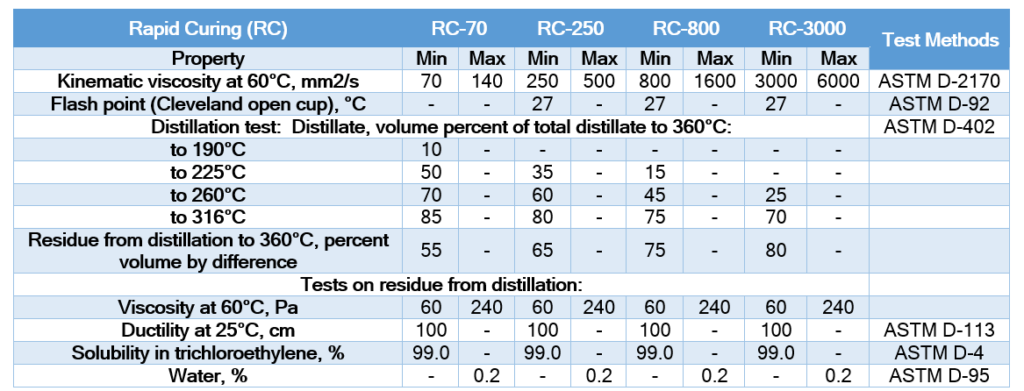
Medium Curing Cutback Bitumen Specification (ASTM D2027 or AASHTO M82-75 2008)

Slow Curing Cutback Bitumen Specification (ASTM D2026)
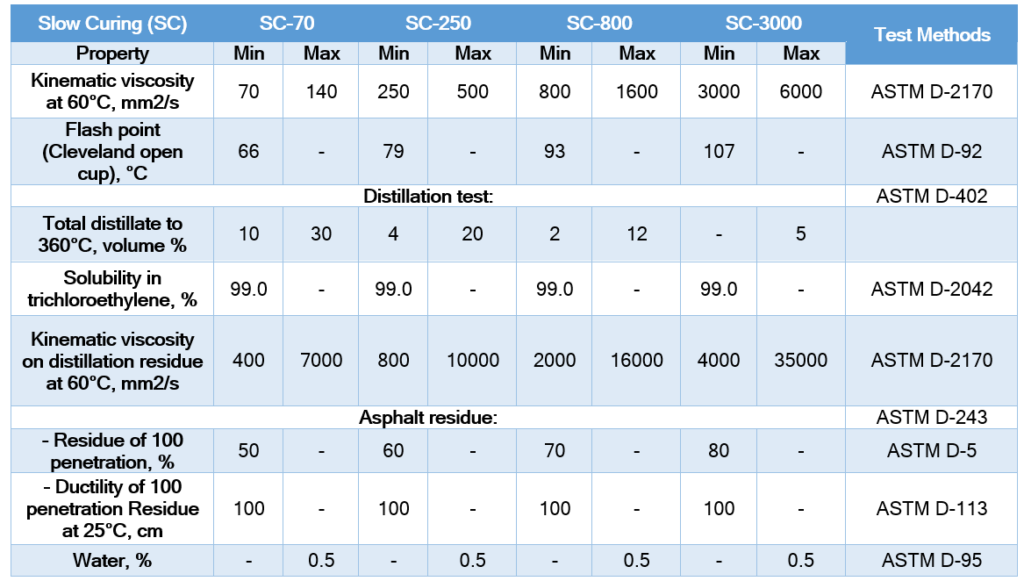